Location
Grande Prairie, Alberta, Canada
Area of Service
HDPE Fusing
Sector
Oilfield Services
Fusing HDPE (high-density polyethylene) pipe is a Ketek specialty
HDPE, or high-density polyethylene, is a flexible plastic pipe used for fluid and gas transfer and is often used to replace ageing concrete or steel mains. Its impermeability and strength make it suitable for high pressure pipelines. HDPE pipe is used around the world for things like water mains, gas mains, sewer mains, slurry transfer lines, rural irrigation, fire system supply lines, electrical and communications conduits, and stormwater and drainage pipes.
For this job, Ketek was fusing HDPE pipe that was 20 inches in diameter. It came in 55-foot lengths which we “butt fused” together. The operator of the butt fusion machine first machines the pipe to make the two ends perfectly flush. He then heats them to a set temperature (in this case, 429 degrees Fahrenheit), which renders the ends molten. He then presses them together with a pre-determined force (384 psi) for a set time to let them cool. It results in a great joint and has similar performance characteristics to the pipe itself.
The field conditions under which HDPE pipe is welded have a considerable effect on the strength of the joint. Three elements are essential for an acceptable weld:
- Cleanliness, because contamination will ruin joints
- Technique: People performing butt fusion must be trained and qualified
- Well designed and maintained equipment: Correct welding temperatures, procedures and pipe facing tools must be used.
For this job, the operators fused 10 lengths together for a 550-foot “drag section” that weighed about 33,000 pounds. A track hoe then dragged the lengths into position, where final fuses were done.
This line, though considered temporary, is expected to be in service for at least 10 years. HDPE pipes can easily be in service for 50 years and more.
Slideshow
The operators machine the ends so they’re flush, then heat them (to 429 degrees Fahrenheit) and press them together (to 384 psi) to create a permanent fuse.
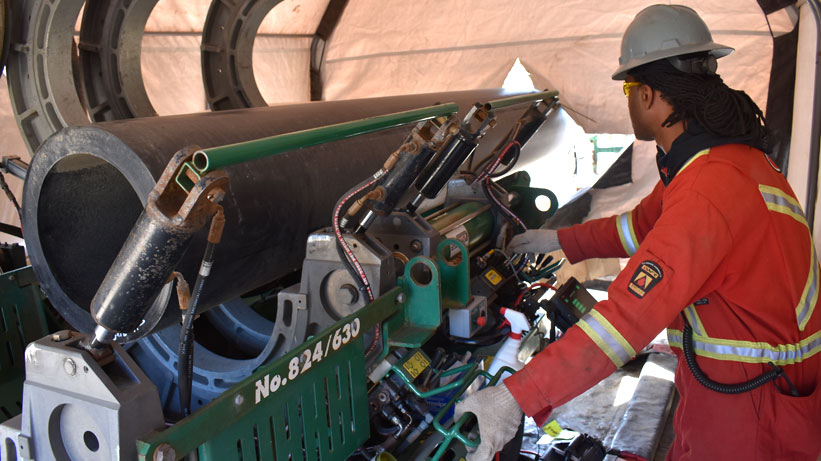
The track hoe pulls the pipe along after each length is added, then drags a section of 10 lengths to its place in the line.
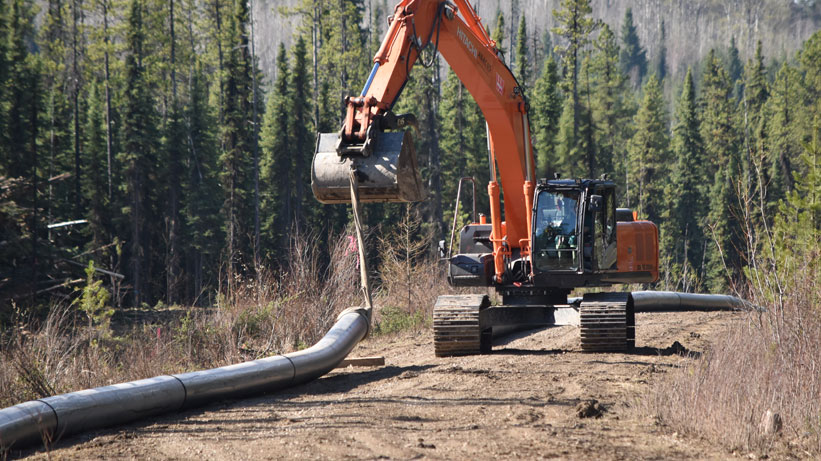
For this job, we had four butt-fusing machines operating.
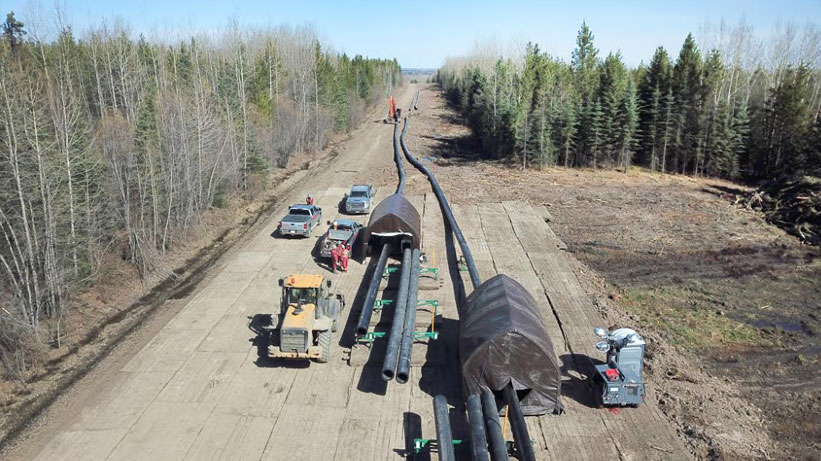
The pipe came in 55-foot lengths, each weighing about 3,300 pounds.
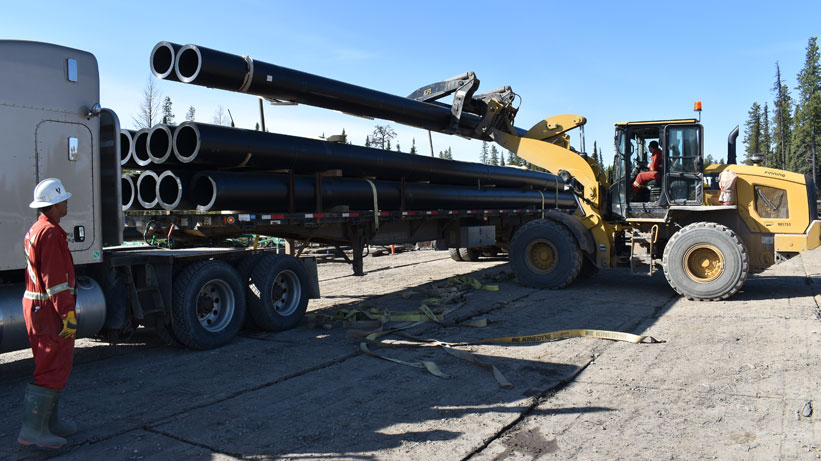
The operators machine the ends so they’re flush, then heat them (to 429 degrees Fahrenheit) and press them together (to 384 psi) to create a permanent fuse.
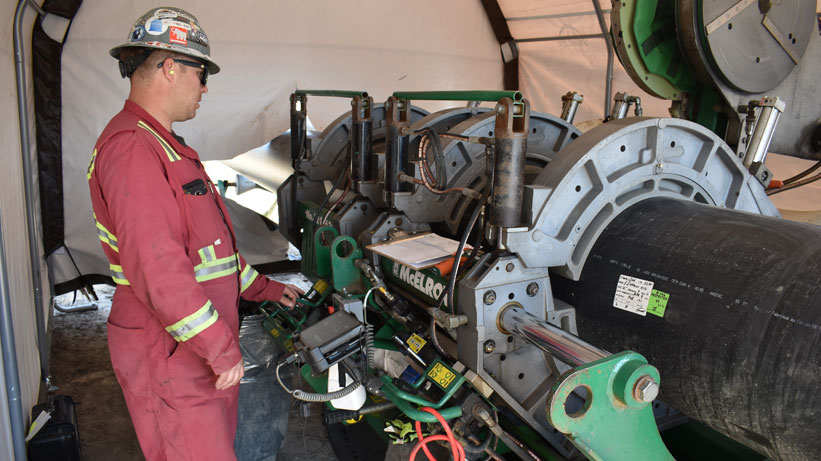
We were fusing HDPE pipe that was 20 inches in diameter.
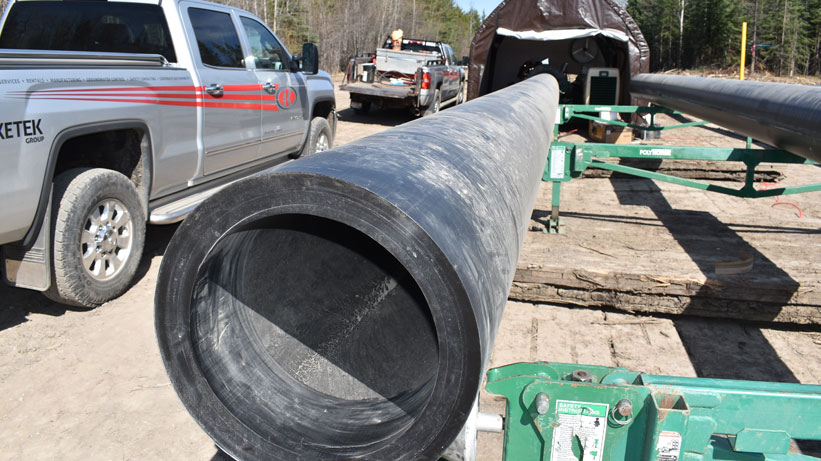
The line came down a steep embankment to the river from which water was being drawn. We fused at the top of the embankment and dragged the line down the hill.
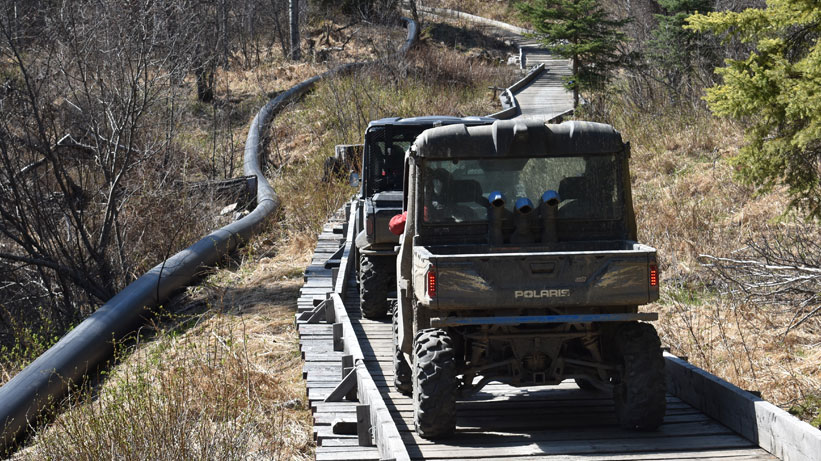