Incineration
Ketek’s Cyclonator incinerators can be an important and effective component of an environmentally friendly waste management system. This is particularly so for remote or small communities.
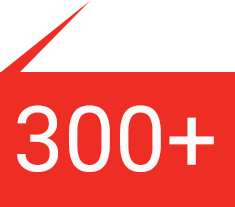
incinerators
around
the world
Ketek has long been a global leader in the manufacture of incinerators. Our Cyclonator incinerators are the preferred solution for waste disposal in dozens of communities and at hundreds of oilfield, mining, hospital and military sites.
Why Incinerate?
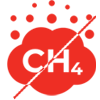
Reduce Greenhouse Gases
By simply moving from landfill to incineration you can reduce GHG emissions by more than 30%.
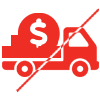
Eliminate Transportation Cost
We can put the incinerator where the waste is generated to eliminate the cost of transportation waste to central landfills and the risks of handling hazardous materials.
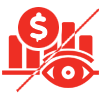
Reduce Landfill Monitoring Cost
The cost associated with a landfill can be exorbitant and includes: air monitoring, surface water, groundwater, leachate.
Ketek’s Cyclonator Incinerators – manufactured to customer specifications at our fabrication plant in Edmonton, Alberta, Canada
Reduce the Waste Volume
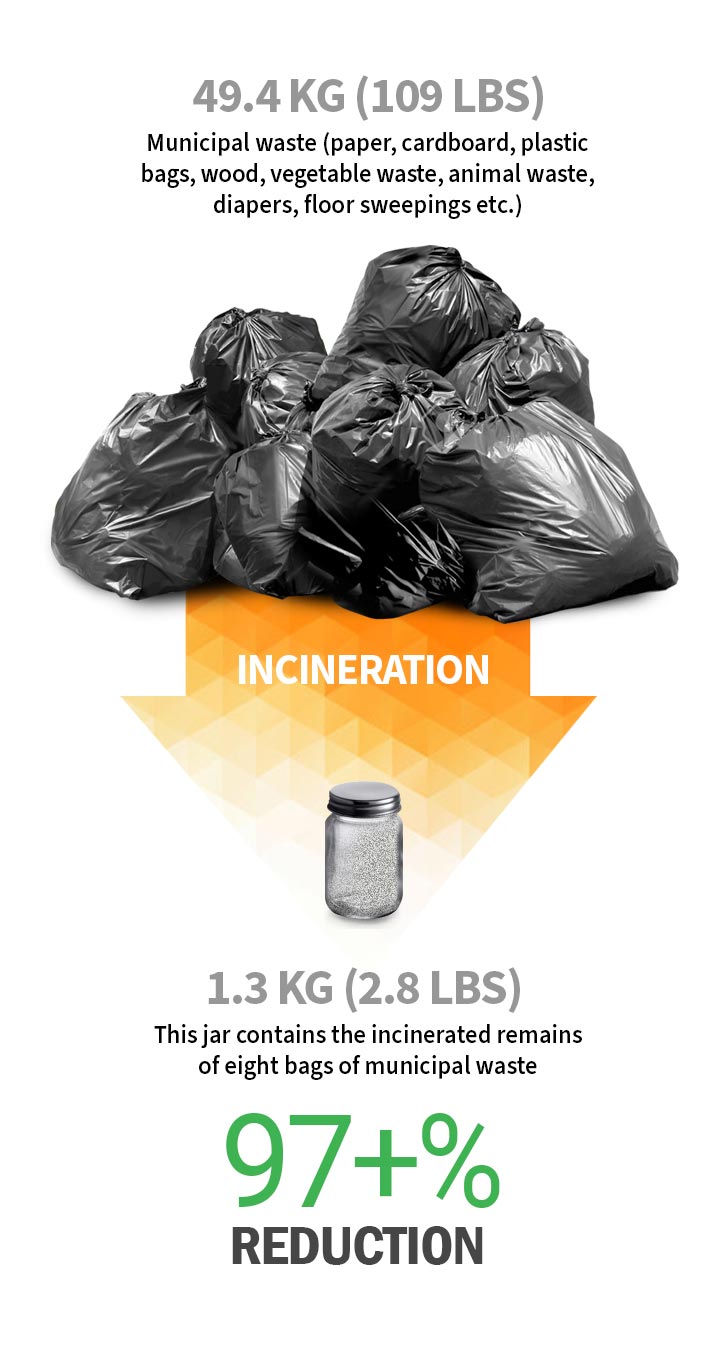
Reduce the Waste Volume
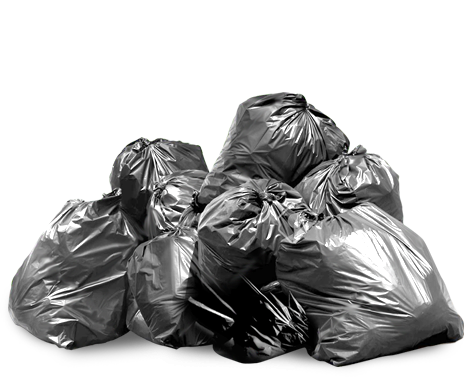
INCINERATION
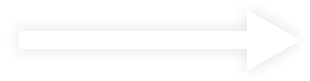
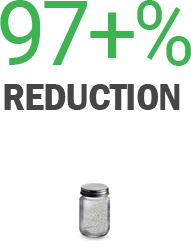
49.4 kg (109 lbs)
Municipal waste (paper, cardboard, plastic bags, wood, vegetable waste, animal waste, diapers, floor sweepings etc.)
1.3 kg (2.8 lbs)
This jar contains the incinerated remainsof eight bags of municipal waste
Composting
Composting recycles carbon, mitigates climate change and feeds the soil. Recycling organic wastes into compost can benefit the environment and people by locking carbon in soil, returning nutrients to degraded land and supporting food security and improved nutrition.
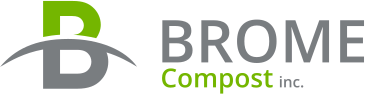
Brome Modular Composter
Efficient on-site modular composting systems that adapt to your needs
The BROME industrial rotating composter is built to optimize the conditions necessary for making compost based on your particular needs, yet remains low maintenance and easy to operate. The components of a modular composter can be modified and assembled to meet a variety of composting needs.
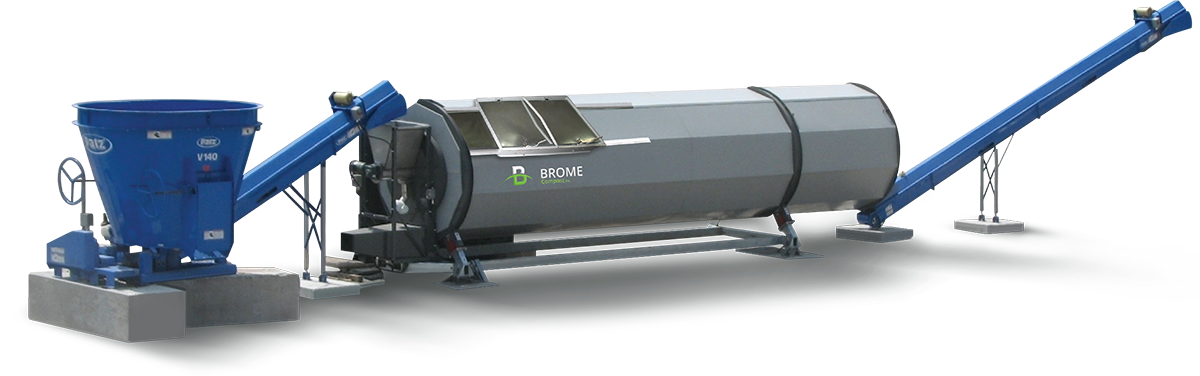
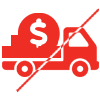
Cost Effective
Save on transport, treatment, storage and landfill costs for all your compostable materials.
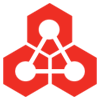
Modular Solution
The system is designed to offer you an efficient integrated solution.
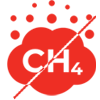
Reduce Greenhouse Gases
Removing organic waste from the regular municipal solid waste stream reduces the production of greenhouse gases (methane).
Our Partner
AltRoot diverts municipal organic waste from landfills and quickly turns it into nutrient-rich, environmentally friendly compost. It then provides that compost to local farmers, who apply it to their fields as a natural fertilizer.
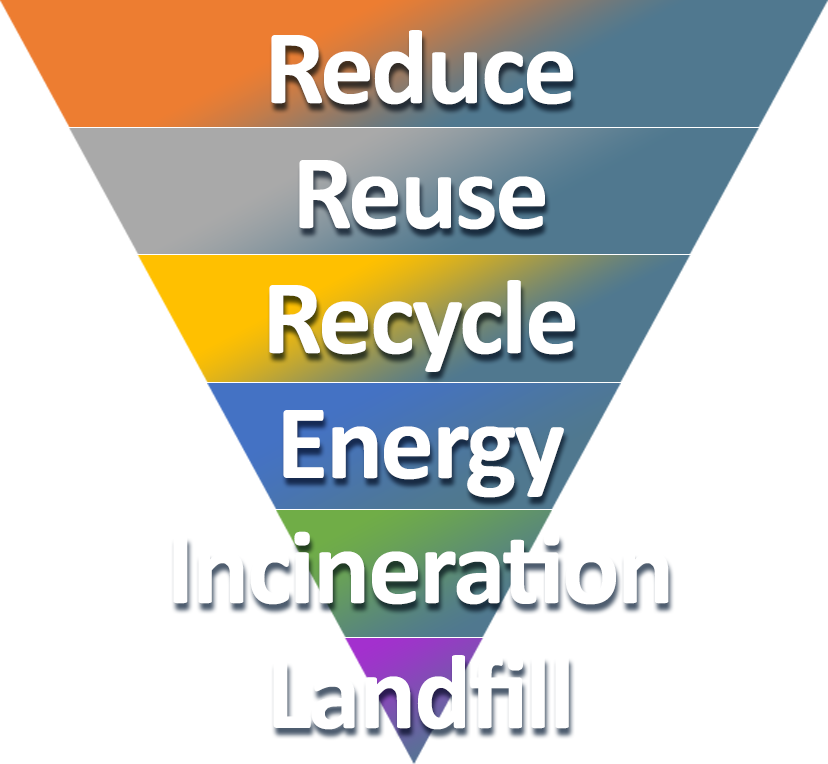
Solid Waste Management
In the waste management industry, you will hear about the “waste hierarchy,” which is dominated by the three Rs of reduce, reuse, and recycle. These are the best ways to properly manage waste and to make a positive impact on our environment. But there are more than just those three layers in the waste management hierarchy. It also includes waste-to-energy, incineration and landfill.
The hierarchy creates guidance for a sustainable waste management program. It is important to understand each of these layers and to find ways to move up the triangle.
That’s where Ketek’s waste management team can help. Accredited by ECO Canada, we offer training for waste audits to help you better manage your waste.
Pollution Control Systems
When it comes to dealing with stack emissions from incineration, Ketek deploys two main technologies depending on the waste, environmental regulations and location of the units: wet scrubbing and dry scrubbing. Both are safe, environmentally friendly options.
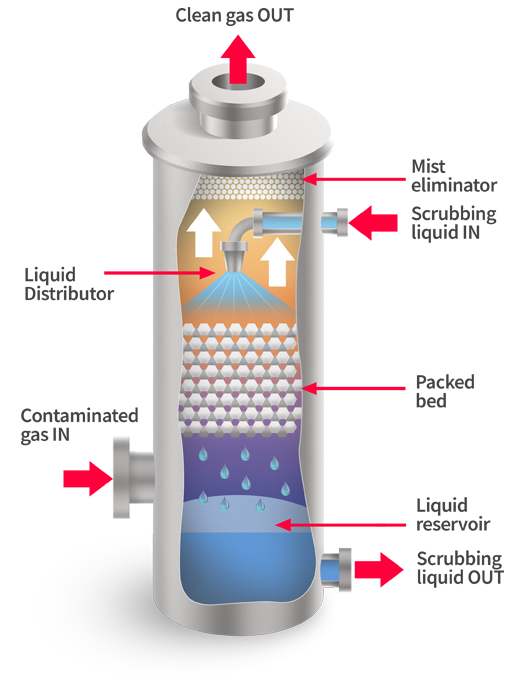
Fish Screens
Most aquatic organisms such as fish and plants cannot come into contact with the pump or the suction hose because they are protected by the screen. A fish screen is placed at a water diversion to protect juvenile fish from entering irrigation channels. They are specifically designed to reduce fish mortality and stranding. Fish screening provides a unique opportunity to increase survival of ESA-listed fish species while allowing irrigators to withdraw water.