Dewatering Techniques and Solutions
The intent of dewatering is to lower and control the water table.
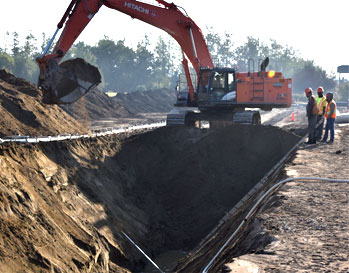
Dewatering refers to the removal of groundwater from soil so excavators can safely and effectively dig trenches and excavations for pipelines, foundations, shoring and cellars.
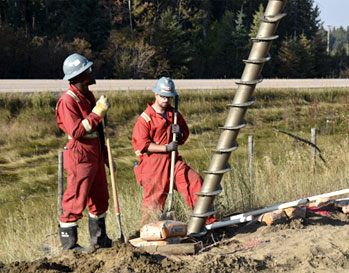
Dewatering involves the use of pumps in wells drilled deep into the earth or, for shallower excavations, the application of vacuum to wellpoints.
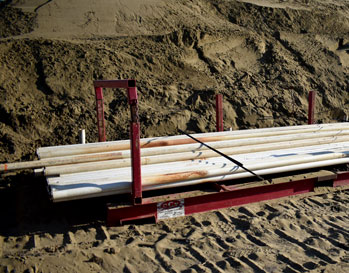
Wellpoints are long, thin pipes that can be stuck in the ground and, like a straw, used to lift water from the Earth. Dewatering will stabilize the slope of an excavation and allow proper compaction of underground facilities.
Three primary methods of dewatering
1. Deep Well Pumps
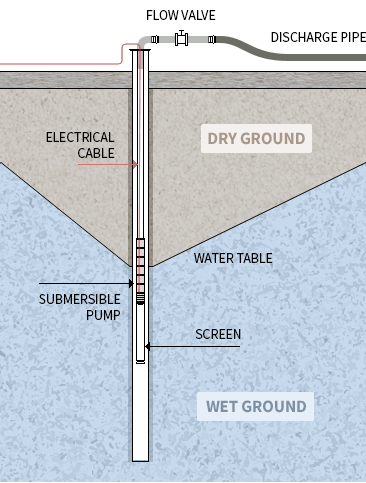
Dewatering via deep wells uses the same drilling and pumping technologies as water supply wells, but in this case the goal is to remove the groundwater. To create the necessary “cone of depression,” several wells are drilled close to each other and fitted with submersible pumps. Working together, they create a hydraulic gradient and water is drawn to the wells. As pumping continues, the cones of depression expand, lowering the local water table.
Deep wells enable excavations to be made safely and effectively and are often required before excavations for pipelines, foundations, shoring and cellars. Deep-well dewatering will stabilize the slope of an excavation and allow proper compaction of backfill for underground facilities.
The wells are drilled just outside the area of the proposed excavation, every 20 metres or so, depending on the project requirements. Electric submersible pumps with riser pipes attached are lowered into the wells. These pumps have small diameters so they can fit down the wells, which are usually between 12 and 35 centimetres in diameter, depending on the flow rate required to dewater effectively.
The most common form of pumping is by electric submersible pumps, which are lowered inside a screen so water can flow more freely. Large drawdowns can be achieved, depending on the number and depth of the wells drilled and hydrogeological conditions.
Deep well dewatering is normally suited to relatively deep excavations (more than five metres) in soil or rock where permeability is either moderate, like sand, or high, like gravel. For shallower excavations, wellpoint dewatering may be the way to go.
2. Vacuum Wellpointing
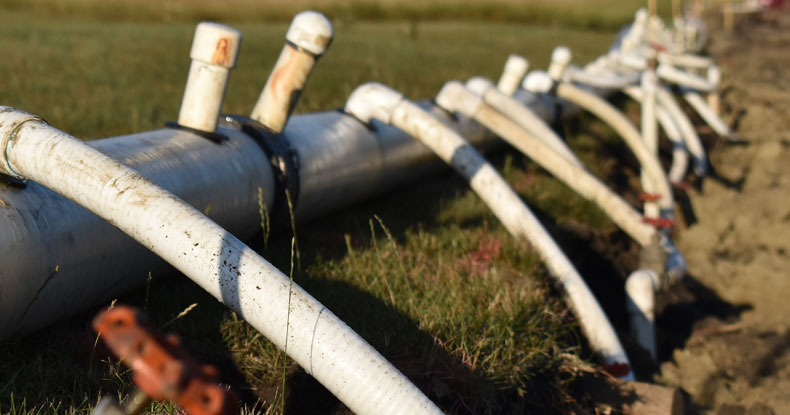
Wellpoints are small diameter pipe made from PVC or steel, up to seven metres long (think of them as giant straws) with a screen or small slits cut in the bottom half-metre. They are installed, one or two metres apart, about one metre from the edge of the excavation. First, holes are drilled or water jetted into the ground. Then filter sand is poured around the wellpoint to filter out fine silt from entering the system and plugging the screen. The wellpoints are connected through a series of swing joints and header pipes to a vacuum system.
The maximum vacuum level is affected by altitude, so the drawdown ability of a single-stage system is typically about 5.5 metres. Systems can be installed in multiple stages to overcome this limitation.
Dewatering this way will stabilize the slope of the excavation allowing for a smaller hole and eliminate the need for a shoring box in many cases as well as reduce the amount of material being removed, saving time and money.
This method of dewatering is heavily used and efficient for open trench excavations, directional drilling receiving pits and remediation projects. Once the excavation is backfilled, the wellpoints are removed. View case study
3. Sump Pumps
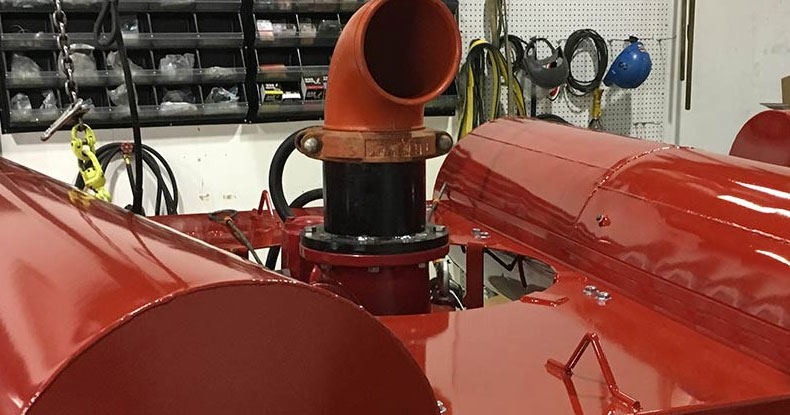
Dewatering can also be achieved by constructing sumps and using either electric submersible or diesel centrifugal pumps installed in the sump to lower the groundwater as well as capture surface runoff.
Automation and Controls
All Ketek pumps can be fitted with either start/stop float controls or water level pressure transducers linked to a variable frequency drive. Pumping systems can be remotely controlled and data can be logged.
Dewatering in mines
Mines must always be aware of water management. Controlling and removing water in a mine, which may run hundreds of metres underground, requires a high level of skill and specialized equipment. Mine dewatering presents some unique challenges in that water volume may be large, the safety of workers is paramount and the integrity of the mine itself is a significant consideration, and water discharged from a mine may not be fit to discharge into the environment.
Fortunately, there are solutions to these problems. Ketek has the means to dewater mines properly and responsibly.